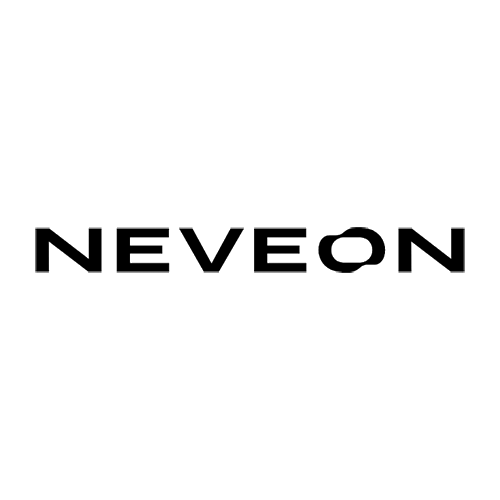
NEVEON Holding GmbH is a company for the production and processing of flexible and composite polyurethane foams. In 2021, the company was founded under its current name and merged as part of Greiner AG from Eurofoam, Greiner aerospace, Greiner Multifoam, Greiner Perfoam, Greiner Purtec and Unifoam.
Creating homogeneous processes when 6 companies merge into one
In 2022, Philipp Hartlauer and his core team of project managers were given a mammoth task: to implement a global project management process that could be applied across NEVEON. The necessary reorganization was an opportunity, it was quickly agreed. This was followed by an evaluation of various project management tools – including Projectworx, which was already in use in other areas of Greiner AG.
Stage-gate model for transparent processes
When I took over as head of the project management department, one of my first observations was that data was being filed twice or even three times, and that there was no real system behind it all,” recalls Hartlauer. In this way, it is hardly possible to map content and requirements efficiently and without errors. In addition, there were all sorts of process descriptions in circulation – countless documents with cross-references to other sub-processes – and no standardized filing system. If you really wanted to follow the defined processes, you would have had to wade through them all. That is simply not practical.
A solution was to be found that did not require a manual. A user-friendly solution with which individual process steps and their documentation can be mapped directly in the tool.
High demands from OEM customers in the mobility sector
“It was also important for us to focus more on the customer during the project management process. Especially in the mobility sector, where we are very customer-oriented and have high requirements from OEMs. Especially in the automotive sector, where IATF certification is a prerequisite and VDA audits are regularly carried out by the customer.
Such an audit was recently scheduled during the implementation of new processes within Projectworx.
“We had a customer audit from a large OEM – a VDA 6.3 audit in the areas of project management, product development and quality, as well as industrialization. This clearly showed how much more agile we are after the reorganization of the processes.”
VDA 6.3 Process Audit: Required measures implemented in the shortest possible time
Resource planning was a key topic in the VDA 6.3 audit. It not only takes capacitive resources into account, but also personnel resource planning: How is it ensured that project employees have the resources they need to complete their tasks on time and with the appropriate quality?
“That was a big question that I honestly couldn’t have answered before. Except that I talk to my people all the time and I know what they’re doing. I could have referred to the fact that we book the hours in SAP – but that’s just the way it was in the past. Thanks to Projectworx, this will change in the future: I can plan the required resources in advance, react to bottlenecks and ensure optimal capacity utilization. This was welcomed by the customer. The order: “Continue with the implementation as planned.
The audit also uncovered potential for improvement. “If nothing was found, then the auditor didn’t do his job properly,” says Hartlauer with a smile. “It was nothing major. It was a quality issue, a procedural issue. And we integrated it into our templates within half an hour the next day. In just a few simple steps, we were able to adapt the process flow, distribute the tasks, use gate logic – and make the newly defined tasks available immediately. With the old system, it would have been a huge effort to rewrite and approve all the documents involved. Projectworx got us there in half an hour.”